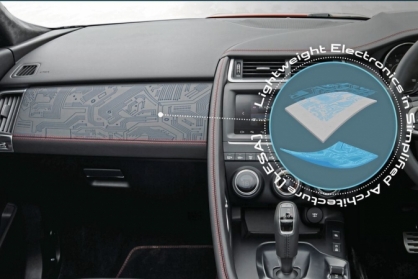
Die Elektronik beansprucht im vernetzten Fahrzeuginnenraum viel Platz und drückt aufs Gewicht. Jaguar Land Rover hat hier eine Technologie entwickelt, die auch bei den Zulieferern ankommt.
Gewichtseinsparungen von bis zu 60 Prozent und bis zu 14-mal flachere Teile: Was sich nach ferner Zukunft anhört, könnte schon in Kürze serienreif sein. Die beeindruckenden Zielwerte stammen von Jaguar Land Rover (JLR) und beziehen sich auf Elektronikprodukte für Fahrzeugcockpits. Der britische Premiumhersteller greift den Trend zu radikal anderen Innenräumen auf und will selbst Akzente setzen. Dabei steht aus Sicht von JLR der Nutzer im Mittelpunkt: Dieser wolle im Fahrzeuginnenraum noch mehr Personalisierung und auf mechanische Knöpfe verzichten. Er erwarte eine individualisierbare Ambiente-Beleuchtung und noch dünnere, aufgedruckte Displays oder eingegossene Sensoren, so wie er es von Produkten aus der
Consumerelektronikwelt gewohnt sei. Das alles fordere auf der Herstellerseite leichte, kleine und vor allem flexibel gestaltete Packages.
Vorbild Consumerelektronik
So viel zur gut klingenden Theorie. Doch JLR trommelt nicht nur mit Marketing für seine Vision, sondern hat auch eine eigene Technologie namens „LESA“ (Lightweight Electronics in Simplified Architecture) konzipiert. Inspiration gaben unter anderem flexible „Wearables“ und gebogene TV-Bildschirme in OLED-Technik aus dem B2C-Bereich. Ashutosh Tomar, Technology Transformation Manager bei Jaguar Land Rover, erklärt den Ausgangspunkt: „Wir mussten den Zielkonflikt lösen,
mehr elektronische Inhalte im Fahrzeug abzubilden und gleichzeitig den Insassen dort mehr Raum zu bieten. Dabei haben wir erkannt, dass es eine existierende Technologie gibt. Unser Job war es dann, diese in die automobile Welt zu überführen.“ Mit „existierender Technologie“ meint Tomar die sogenannte strukturierte Elektronik, von der neben der Verbrauchertechnologie auch schon das
Gesundheitswesen, die Luft- und Raumfahrt sowie die Militärindustrie profitieren.
allem Gewichtseinsparungen bringt. Zudem entfallen sperrige Steuergeräte, und das Package verkleinert sich. Die Entwicklungsabteilung des Herstellers hat zudem über Kapselung die Haltbarkeit von Sensoren erhöht, die so besser gegen Erschütterungen, Feuchtigkeit und Ablagerungen
geschützt sein sollen. Im Detail wird bei der Herstellung der Systeme über CAD (Computer Aided Design) das jeweilige Bauteil zunächst „aufgefaltet“. Der elektronische Schaltkreis – der nach bisheriger Methode in einem konventionellen Steuergerät verkabelt wurde – wird dann auf die flache Oberfläche gedruckt und die Komponenten werden montiert, ehe die CAD-Darstellung in das 3-D-Original zurückgeht. Das Teil inklusive der auf der Oberfläche aufgedruckten Elektronik ist damit bereit für die Serienproduktion. Jaguar Land Rover hat die LESA-Technologie schon erfolgreich an einem Prototyp
für ein Overhead-Bedienpanel getestet. Dabei wurde nicht nur Masse eingespart: Auch die Dicke schrumpfte von 50 auf 3,5 Millimeter.
Elektronikherstellern zu erklären, wie man beide Themen zusammenbringt. Laut Tomar wurde schnell deutlich, dass verschiedene Tier-1-Supplier den JLR-Ansatz und die Prozesse dahinter sehr interessant
finden oder sogar schon umsetzen.
© Text:
www.automobil-industrie.vogel.de/wearables-als-vorbild-jlr-drucktelektronik-
a-907637/
Autor/ Redakteur: Christian Otto / Maximiliane Reichhardt
© Foto: Jaguar Land Rover